デジタルツイン入門:現場と仮想空間をつなぐシステム開発の基礎知識
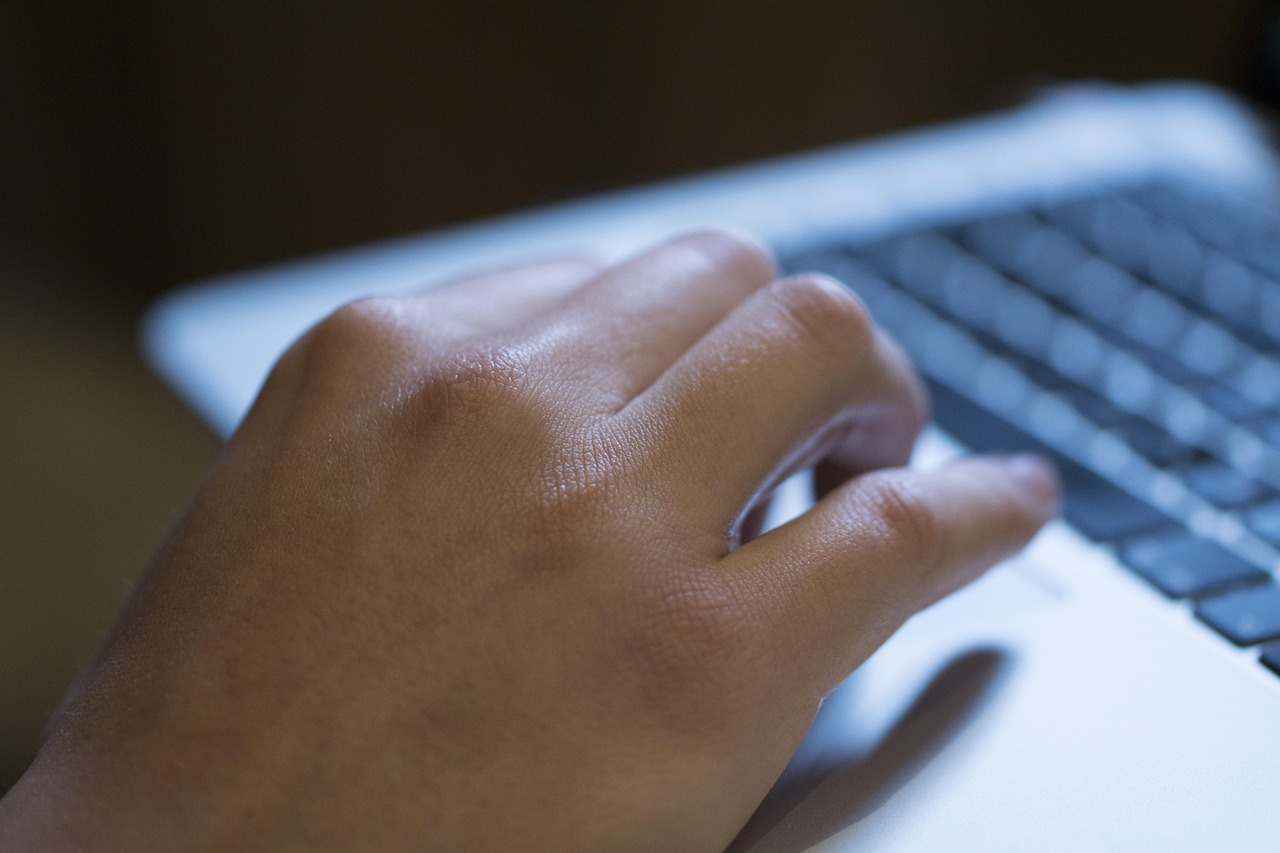
デジタルツインとは何か?
「デジタルツイン」とは、現実世界の物理資産やプロセスを仮想空間上に再現し、リアルタイムに連動させる技術です。製造ライン、ビル設備、インフラ機器など、多種多様な対象をデジタル上で“双子”として扱い、シミュレーションや分析を行います。IoTセンサーで収集した稼働データをもとに、デジタルツイン上で故障予測、最適運転、遠隔監視などを実現。
-
用途例
-
製造装置の稼働率最適化
-
建物設備の省エネシミュレーション
-
自動車部品の疲労解析
-
デジタルツインは、単なる可視化ではなく、仮想空間での高度な解析・自動制御が特徴。これによりビジネス上の意思決定が迅速化し、トータルコスト削減につながります。
なぜ今、デジタルツインが必要とされるのか?
従来のシステムではデータを蓄積・レポートするだけで終わりがちでしたが、DX(デジタルトランスフォーメーション)時代には「取得したデータをどう活用するか」が問われます。デジタルツインを導入するメリットは以下の通りです。
-
リアルタイムモニタリング
-
センサー故障や制御系の異常を即時検知し、稼働停止や品質低下を防止。
-
-
予知保全
-
過去の稼働データと機械学習を組み合わせ、故障発生前にメンテナンスを実施。
-
-
運転最適化
-
仮想空間で各種パラメータをシミュレーションし、エネルギー消費や生産効率を最大化。
-
-
遠隔協調
-
複数拠点の装置を一つの仮想プラットフォームで統合管理し、ナレッジを横展開。
-
これらによって、設備投資効率の向上やOPEX(運用コスト)の圧縮など、投資対効果(ROI)の最大化が可能になります。
デジタルツイン構築の基本アーキテクチャ
デジタルツインを構築する際の典型的なアーキテクチャは、以下の3層構成です。
-
エッジ層
-
IoTゲートウェイやPLC(プログラマブルロジックコントローラ)でセンサーデータを収集、一次処理(フィルタリング、圧縮)。
-
-
プラットフォーム層
-
クラウドまたはオンプレミスのデジタルツインプラットフォームで、時系列データベースに格納し、解析モデルを適用。
-
-
アプリケーション層
-
ダッシュボードやモバイルアプリで可視化、アラート通知、シミュレーション操作パネルを提供。
-
各層をつなぐための通信プロトコル(MQTT, OPC-UA, HTTP/REST)や認証・暗号化設計も、システム開発会社選び方の重要ポイントです。
要件定義のポイント:成功するプロジェクトへの第一歩
デジタルツイン導入プロジェクトで失敗しないためには、要件定義フェーズが極めて重要です。以下の点に留意しましょう。
-
業務フローの可視化
-
現場担当者と一緒に、どのタイミングでどのデータが必要か洗い出す。
-
-
KPI設定
-
モデル精度、異常検知時間短縮率、省エネ率など、定量的な評価指標を明確化。
-
-
フェーズ分割
-
PoC→本格開発→運用という段階的アプローチでリスクを低減。
-
-
予算感の擦り合わせ
-
ハードウェア費用、クラウド利用料、システム予算(開発工数×単価)などを初期段階で概算。
-
-
ベンダー境界の明確化
-
プラットフォーム提供ベンダー、AIモデル開発ベンダー、UI/UX開発ベンダーなど役割分担を明示。
-
これらを踏まえたRFP(提案依頼書)を作成し、複数社からの見積もりを比較することで、適正な費用相場を把握できます。
PoC/プロトタイプのすすめ方
要件定義後は、必ずPoC(Proof of Concept)を実施して、データ収集・モデル適用・ダッシュボード検証の可否を早期に判断します。PoCの流れは次の通りです。
-
対象設備の選定
-
リスクが低くデータが取りやすい装置を1~2台ピックアップ。
-
-
センサー実装とデータ収集
-
必要な物理量(温度、振動、流量など)を測定し、最低2週間はデータを溜める。
-
-
初期解析・可視化
-
データに欠損やノイズがないかチェックし、BIツールでプロトダッシュボードを作成。
-
-
モデル試作
-
簡易的な異常検知モデルや回帰モデルをクラウド環境で動かし、初期精度を確認。
-
-
成果検証
-
KPI達成度をPDCAサイクルで検証し、次フェーズの要件修正を実施。
-
PoC段階で技術的なネックや追加発注要件を洗い出し、本稼働時の手戻りを防ぎます。
本開発フェーズの留意点
PoC成功後、本番システムとして開発を進める際は、以下を徹底します。
-
スケーラブルなアーキテクチャ
-
IoTデバイス数やデータ量が増えても対応できるクラウド基盤(コンテナ、サーバーレス)を採用。
-
-
高可用性設計
-
マルチAZ構成、データベースのリードレプリカ、エッジ冗長化などでSLAを担保。
-
-
CI/CD導入
-
ソースコード管理と自動テスト、自動デプロイをパイプライン化し、品質と開発スピードを両立。
-
-
運用・保守ドキュメント
-
デバイス管理手順、トラブルシュートフロー、緊急連絡先一覧などを整備し、現場と開発会社で共有。
-
-
教育・トレーニング
-
現場担当者向けに操作マニュアルやハンズオントレーニングを提供し、定着化を図る。
-
これらの施策を盛り込むことで、本番運用開始後の追加費用やトラブル対応コストを最小限に抑えられます。
実際の導入事例:製造ラインのデジタルツイン活用
とある製造機械メーカーA社では、デジタルツインを導入し、ライン停止による年間1,000万円超の損失を防ぐことに成功しました。以下がプロジェクト概要です。
-
課題認識
-
月に数回発生するライン停止が原因で、大量の手戻りと品質検査コストが発生。
-
-
PoCフェーズ
-
3台の工作機械に振動・温度センサーを取り付け、2週間でデータを蓄積。
-
クラウドで異常検知モデルを試作し、既知異常95%を検出。
-
-
本格開発
-
データ取得からアラート通知までのエンドツーエンドをスケーラブルに設計。
-
UI層に製造現場向けのカスタマイズダッシュボードを提供。
-
-
運用結果
-
導入後6ヵ月でライン停止回数が50%減少、年間で1,200万円のコスト削減を実現。
-
この事例では、要件定義で“検出精度90%以上”“アラート遅延200ms以下”などのKPIを明確化し、PoCで早期に技術適合性と費用相場を確認したことが成功要因でした。
ROI試算の具体的手順
デジタルツイン導入の予算判断に必須なのがROI(投資対効果)の試算です。以下のフレームワークで概算を行いましょう。
-
削減コストの算出
-
現状ライン停止による1回あたり損失額×年間停止回数
-
-
導入コストの合計
-
ハードウェア費用+ソフト開発費(人日×単価)+クラウド利用料+運用保守費
-
-
回収期間(Payback Period)
-
導入コスト ÷ 年間削減コスト
-
-
累積キャッシュフロー
-
各年の削減コスト-運用保守費の累計
-
項目 | 金額(万円) |
---|---|
年間停止損失削減額 | 1,200 |
初期導入コスト(2年償却) | 800 |
年間運用保守費 | 120 |
回収期間 | 約0.67年 |
この試算により、A社は1年以内に投資回収できると判断し、発注を決定。経営層も納得の上、スムーズにプロジェクトを進行できました。
拡張フェーズ:AI最適化と業務自動化
デジタルツインを軸にさらに踏み込んだ拡張フェーズでは、以下のようなAI最適化・自動化を検討します。
-
自動制御ループの実装
-
AIが最適動作点を算出し、自律的に設備パラメータを調整。
-
-
シナリオシミュレーション
-
新製品導入時のライン調整シミュレーションを仮想空間で実施。
-
-
品質予測
-
生成データと検査結果を用いた品質予測モデルを追加し、検査工程の自動スキップ判断。
-
これらにより、さらなるDX効果を創出するとともに、次期プロジェクトでも再利用可能な技術資産が形成されます。
デジタルツイン導入時のよくあるQ&A
導入にあたって現場からよく寄せられる質問と、その回答をまとめました。
-
Q1: センサー設置先が限定されるが大丈夫?
-
A: まずPoCでサンプリング箇所を決め、効果が高いポイントを重点的に測定します。
-
-
Q2: データ量が膨大でクラウドコストが心配
-
A: エッジ層で前処理・集約し、要約データのみ送信することで通信・ストレージコストを抑制可能です。
-
-
Q3: 既存システムとの連携は?
-
A: ERPやMESとAPI連携し、製造指示や在庫情報をデジタルツイン上で統合可。
-
-
Q4: 社内にノウハウがないが自前で運用できるか
-
A: ベンダーの運用支援パッケージを利用し、運用ドキュメント・教育をセットで提供してもらうのがおすすめです。
-
これらのQ&Aを事前にまとめ、RFPに添付して開発会社と共有すると、プロジェクトの認識齟齬を防げます。
今後のトレンド:メタバース/デジタルツイン連携
将来的には、メタバースプラットフォームとの融合が予想されます。ユーザーがVR/AR空間でデジタルツインを操作し、現場を仮想体験しながら意思決定するユースケースが増加中です。
-
ARガイド
-
現場オペレータがタブレット越しに設備内部情報をリアルタイムに閲覧
-
-
遠隔コラボレーション
-
海外拠点と仮想会議しながらライン調整やトラブルシュート
-
-
3Dシナリオデザイン
-
設備改造前に3Dモデルでレイアウト検討、動線最適化シミュレーション
-
この先進的な取り組みは、製造業に留まらず、建設・物流・医療など幅広い業界で応用されるでしょう。
まとめ:新しい基礎知識としてのデジタルツイン
-
デジタルツインは現場と仮想をリアルタイム連動し、予知保全や運用最適化を実現する基盤技術
-
要件定義→PoC→本番開発→運用保守のフェーズ管理が成功の鍵
-
開発会社選び方では、IoT/AI/クラウドなどマルチベンダー連携力を評価
-
ROI試算やQ&Aをもとに、早期発注判断とリスクマネジメントが重要
-
将来はメタバース連携など、更なる拡張が期待できる
デジタルツイン導入は、製造ラインだけでなくあらゆる業務プロセスのDXを加速します。まずは小規模PoCから、未来のワークスタイルを体験してみてください。