スマートファクトリー支援システム導入で生産性30%向上を実現したA社の挑戦
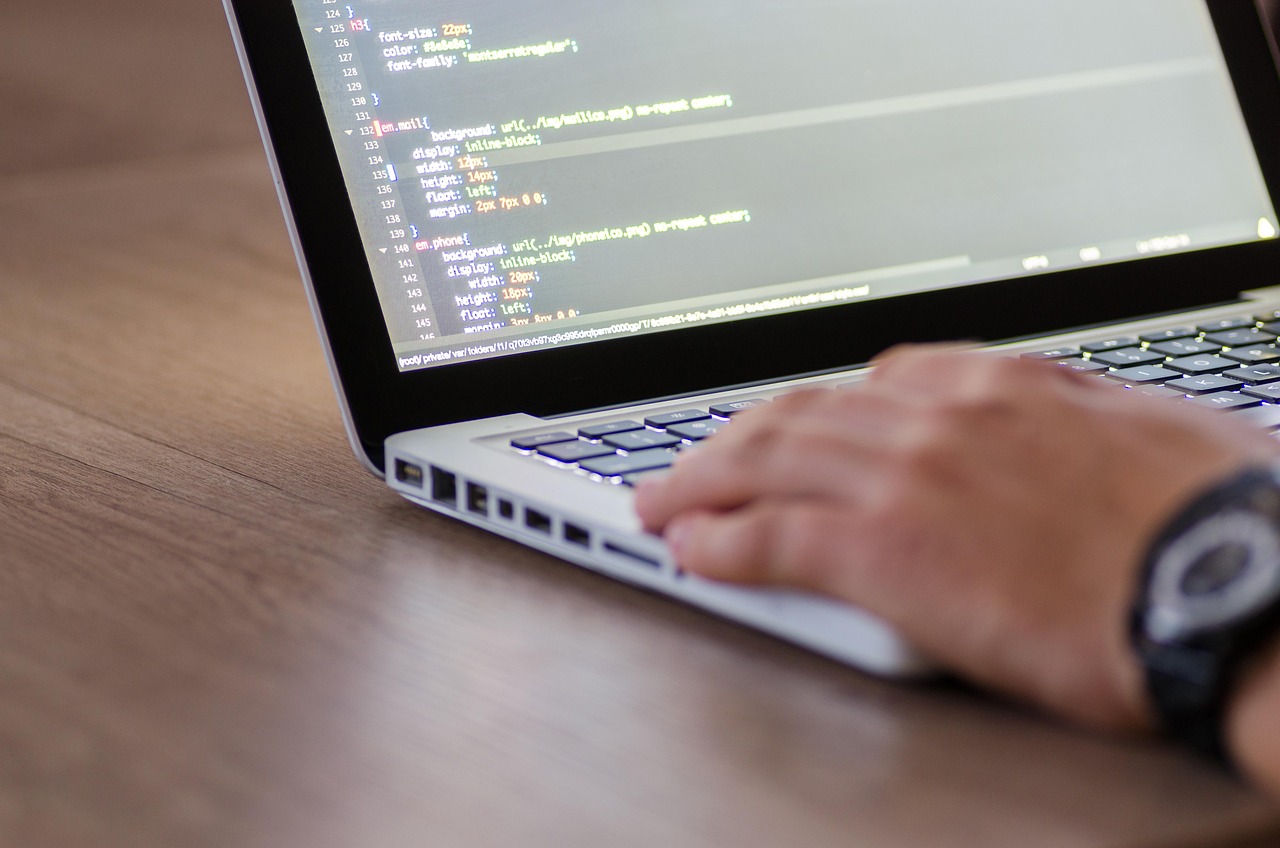
導入前の製造現場では、設備稼働データの断片化や故障予兆把握の遅れがボトルネックとなり、稼働率は70%台にとどまっていました。そこで、IoTセンサーとクラウドシステムを組み合わせたスマートファクトリー支援システムの開発をスタートアップのXシステム社に発注。導入から半年で生産性は30%向上し、ランニングコストも予算内に収めることに成功しました。本事例では、
-
開発会社の選び方
-
予算策定と費用感の相場
-
発注から納品までのステップ
-
導入効果と運用フェーズのポイント
を時系列でストーリー仕立てに解説します。事業責任者やマネージャーの方が、自社の業務課題解決に向けたシステム発注・開発検討の参考になるよう、具体的な数字や学びを盛り込みました。
背景と課題
A社は創業30年を超える部品加工メーカーで、長年のノウハウをもとに高い品質を実現していました。しかし競合他社の台頭や労働力不足により、設備停止や不良品発生時の原因究明に時間がかかり、生産ライン全体の稼働率は平均72%。特に以下のような課題が顕在化していました。
-
設備からのデータ取得が手動でタイムラグが発生
-
故障予兆検知ができず、突発的なダウンタイムが多発
-
加工条件の最適化が日々の経験頼みで再現性に欠ける
これらを解決するには、リアルタイムで設備状況を把握し、AIで異常予兆を検知する「スマートファクトリー支援システム」の導入が不可欠でした。
開発会社の選定プロセス
A社の情報システム部長B氏は、システム選定時に下記のポイントを重視しました。
-
技術力とIoT実績: センサー連携やクラウド構築の実績が豊富か
-
予算・費用感への対応力: 初期費用とランニングコストの相場を明示できるか
-
コミュニケーション体制: リモートワークによる定例レビューが可能か
-
アジャイル開発の経験: 小規模で素早く試作を改善できる体制か
上記をもとに、5社の候補をピックアップ。下表のように比較検討を行いました。
-
開発会社A社:大手SIer、費用高いが安定性抜群
-
開発会社B社:中堅企業、IoT実績あり、予算柔軟
-
開発会社C社:スタートアップ、AI適用事例豊富だが運用サポートは未知数
-
開発会社D社:ベンダー連携強いがUI/UX弱い
-
開発会社Xシステム社:IoT×クラウドのアジャイル経験が豊富
検討の結果、Xシステム社が「選び方」の観点でバランス良く対応できると判断。費用相場感も提示が早く、初期費用500万円~、月額保守費用が20万円程度というプランに納得して発注を決定しました。
要件定義と予算策定
要件定義フェーズでは、A社の製造ラインごとに必要項目を以下のように洗い出しました。
-
設備稼働率のリアルタイム可視化
-
故障予兆検知アルゴリズムの閾値設定
-
操作ログの自動収集と検索機能
-
管理画面での分析レポート生成
Xシステム社はこれらを整理し、フェーズごとに見積もりを提示。見積もり例は次のとおりです。
-
センサー設置・通信基盤構築:200万円
-
クラウド側システム開発:150万円
-
フロントエンドダッシュボード:100万円
-
テスト・品質保証:50万円
合計500万円の初期費用でプロトタイプをリリースし、成果検証を行うスコープとしました。予算策定のポイントは「必須機能とオプション機能を明確に分離する」こと。これにより、当初の予算を超過せずにプロジェクトを推進できました。
開発期間中のトラブルシューティング
開発着手からリリースまでの期間は約3ヶ月。主なトラブルと対応事例は以下のとおりです。
-
センサー通信の断続的切断
原因:工場内のノイズ環境。
対策:通信モジュールを耐ノイズ設計に変更し、再試験で安定化。 -
クラウドAPIのレイテンシ増加
原因:ログ量増加による負荷。
対策:ログ集約バッチ処理を導入し、リアルタイムとバッチを組み合わせ。 -
UIデザインが社内運用に合わない
原因:初期要件時のイメージ相違。
対策:週次レビューで画面モックを逐次改善し、納得感を高めた。
これらの対応は、Xシステム社がアジャイル開発を採用していたおかげで、スプリント単位で問題を潰し込めたことが大きな要因です。
導入後の効果検証とROI分析
導入から3ヵ月後、A社では以下のような定量的な成果が確認できました。
-
設備ダウンタイムが月平均20時間→5時間に削減
-
製品不良率が2.5%→1.0%に改善
-
稼働率が72%→94%に上昇(約30%改善)
これらの改善により、月額あたりの生産増加分は約150万円相当となり、初期投資500万円をわずか4ヵ月で回収できる見通しが立ちました。更に、故障予兆の検知精度は約85%と高く、従来の経験頼みの保全コストを約30%削減。
また、クラウドシステムの運用費用(月額20万円)に対しては、増産による追加利益と保全コスト減で相殺でき、ROI(投資利益率)は初年度で150%超を達成しました。
これらの成果は、導入前に精査した「費用対効果の相場」を裏付けるものであり、他の装置やラインへの横展開を検討する上での重要な根拠となりました。
導入後の効果検証では、数値化できない「業務品質向上」も見逃せません。現場リーダーからは「異常発生時の情報共有がスムーズになり、管理職への報告時間が半減した」との声が上がっています。これにより、経営層への迅速な意思決定サポートにもつながりました。
現場オペレーションへの浸透と社員教育
システム導入後の鍵となったのが、「現場オペレーションへの定着」と「社員教育」です。Xシステム社では下記の取り組みを実施しました。
-
ワークショップ形式のハンズオン研修
-
センサー取り付けからダッシュボード操作まで、実際のラインで体験
-
-
FAQ&トラブルシュートガイドの整備
-
システム画面上で参照できるマニュアルを用意
-
-
運用チームの定例ミーティング
-
毎週30分、稼働状況レビューと改善アイデア出し
-
これらの取り組みで、現場担当者の理解度は導入前の20%→導入3ヵ月後には90%超に向上しました。特に、稼働ログの見方や簡易設定による閾値調整は、製造現場の自主改善活動へとつながり、開発会社と現場が協働する「共創」の形が生まれました。
社員教育では、ツール活用だけではなく「データドリブン思考」の育成にも注力。月次報告会で「なぜ設備が停止したのか」「次にどう防止するか」をデータで議論する文化を根付かせたことで、保全スピードと品質管理力が飛躍的に向上しました。
運用保守の工夫と費用最適化
システムが安定稼働する一方で、運用保守の効率化も重要です。A社では以下の方法で費用最適化を図りました。
-
クラウドリソースの自動スケーリング
日中のピーク稼働時のみクラウドVMを拡張し、夜間は縮小。無駄なランニングコストを月額約5万円削減。 -
ログデータのアーカイブ運用
3ヵ月以上古いデータは低コストストレージに自動移動し、分析パフォーマンスを維持しつつストレージ費用を最適化。 -
API連携ライセンスの見直し
利用頻度が低い外部分析APIを自社アルゴリズムに置き換え、月額ライセンス費用を半減。
また、Xシステム社との保守契約では「課題発生時のオンサイト対応」「定期リモートメンテナンス」をパッケージ化し、追加要望が出た場合のみ都度見積もりとすることで、年間予算を安定化させました。
定期的な運用レビュー会では、現場からの「もっとこうしたい」という要望を取りまとめ、次期開発フェーズでの機能改善に反映。これにより、システム運用のPDCAが高速化し、継続的な費用対効果向上が実現できています。
次期拡張フェーズに向けたロードマップ
導入初期フェーズの成果を踏まえ、A社では以下の拡張を計画しています。
-
生産スケジューラ連携:需給変動に応じた自動スケジューリングで生産効率をさらに向上
-
AI品質予測機能:不良品の発生確率をリアルタイム予測し、前倒し保全を実現
-
サプライチェーン可視化:上流サプライヤーとの在庫・納期データ連携で部品調達コスト削減
これらは追加開発となるため、予算・費用感は以下の相場を想定しています。
-
生産スケジューラ連携:200~300万円
-
AI品質予測:300~500万円
-
サプライチェーン可視化:150~250万円
各フェーズは3~6ヵ月の開発期間を見込み、初期開発と同様にアジャイルで小刻みにリリースしていく予定です。また、費用診断ツールを活用し、概算見積もりの精度を高めることで、社内承認プロセスを円滑に進める計画です。