製造業向けIoT予知保全システム導入事例|コスト削減と生産性向上を実現
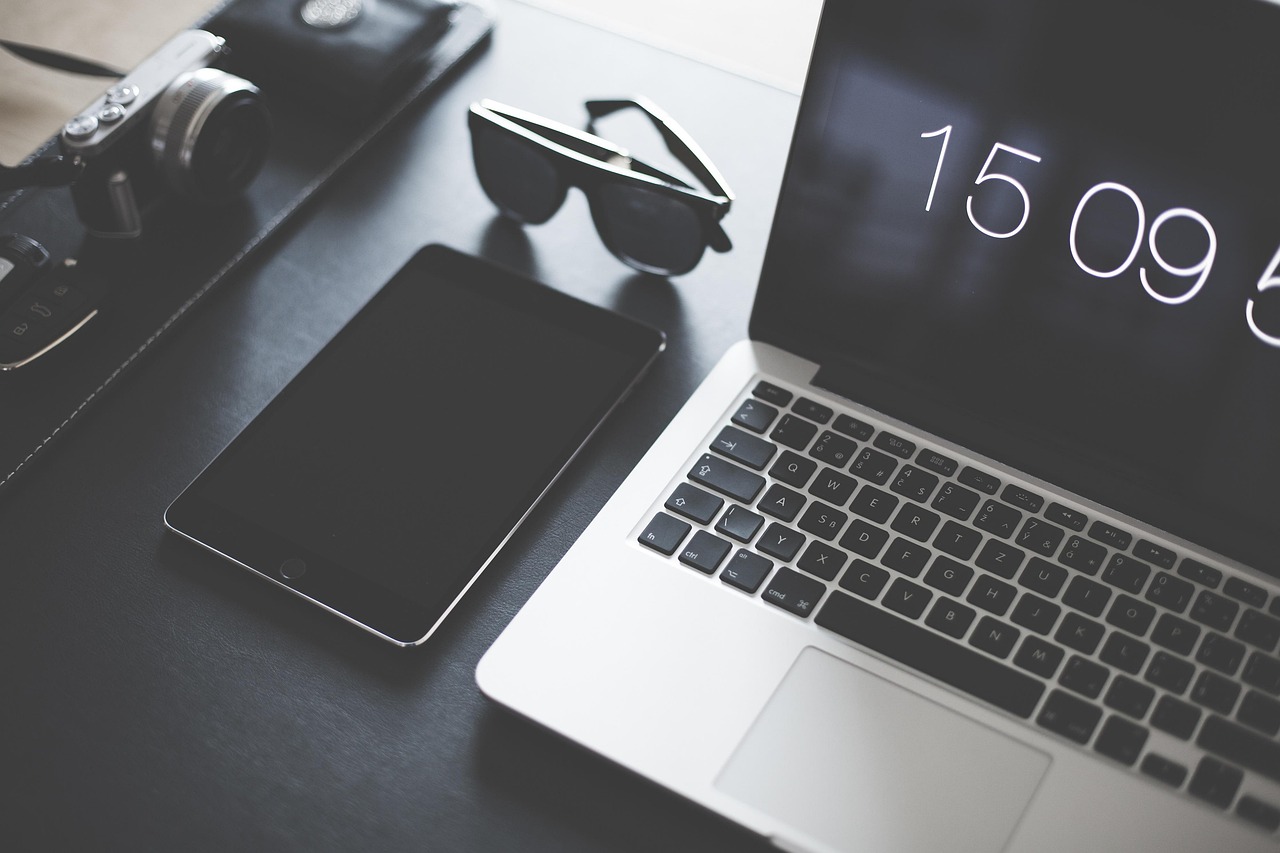
製造ラインの停止は、1時間あたり数百万円の損失につながることも珍しくありません。本事例は、大手精密機械メーカー「テクノプロダクト社」が、故障予兆を検知するIoT予知保全システムを自社工場に導入し、ダウンタイムを50%削減、年間維持費を30%カットしたユースケースです。システム要件の策定から、開発会社選び、予算交渉、発注プロセス、運用開始後の成果まで、時系列で詳細にご紹介します。
課題背景と導入検討の経緯
テクノプロダクト社では、従来の定期メンテナンスが機械の稼働状況に追いつかず、突発的な故障によるライン停止が多発。平均稼働率は85%程度に留まり、予備部品の在庫コストも膨張していました。業務改善部門が実施した現状分析では、以下のような課題が明らかになりました。
-
故障予兆が可視化されず、メンテナンスは「予定」にしか依存できなかった
-
予備部品の発注タイミングが明確でなく、在庫費用が高騰
-
既存のシステムではリアルタイムデータを収集できず、相場感ある運用が困難
これらを受け、IoTを活用した予知保全システムの導入検討を開始。まずは工場内数台の試験導入で効果を検証し、成功を受けて全ラインへの横展開を計画しました。このフェーズでの選び方ポイントは、「PoCに適切なミニマム構成」と「将来の拡張性」を両立できるシステム設計でした。
開発会社選定と予算策定のポイント
開発会社は、機械制御とクラウドサービス双方の知見が求められるため、下記基準で選定を実施しました。
-
ドメイン経験:製造業向け予知保全プロジェクト実績の有無
-
技術スタック:AWS IoT CoreやAzure IoT Hubの利用経験
-
体制柔軟性:要件変更に対応できるアジャイル開発体制
-
費用感:類似プロジェクトの開発費用相場と見積根拠の明示
初期見積もりは約1,200万円(PoC範囲)でしたが、上記基準に合致する3社からRFPを取得し、最終的に「ファクトリーワン社」を選定。交渉ではPoC結果による追加機能をオプション化し、予算超過リスクを抑えつつ、全社横展開まで見据えたライセンス費用を調整しました。最終発注額は1,350万円と、当初予算とほぼ同水準に収めています。
システム設計と機能概要
予知保全システムのアーキテクチャは以下の3層構成です。
-
エッジ層:PLCとセンサーから振動・温度データを収集
-
ミドル層:ゲートウェイでデータ前処理し、クラウドへ転送
-
クラウド層:ストリーム処理+機械学習モデルで異常予測
主な機能は次のとおりです。
-
振動異常検知:FFT解析による振動周波数の変動監視
-
温度急上昇警報:閾値超過時に即時アラート
-
予兆レポート:定期レポートで予備部品発注タイミングを提案
-
ダッシュボード:リアルタイム稼働状況を可視化
システム構築期間はPoCを含めて約4ヶ月。要件定義と並行してテスト環境を整備することで、開発スピードを最適化し、無駄な費用増を防ぎました。
IoTセンサーとデータ基盤構築
センサーは既存機器のM12コネクタから簡単に接続可能な振動・温度一体型デバイスを採用し、配線工数を最小限に。ゲートウェイにはARMベースの産業用PCを選定し、オンプレミスでの前処理を実現しました。
データ基盤は以下の構成で構築。
-
ストリーム処理:Cloud Pub/Sub(GCP)でデータキューイング
-
データレイク:BigQueryに蓄積し、長期間の相場分析を容易に
-
機械学習:AutoMLを使った異常検知モデルの自動チューニング
これにより、データ処理パイプラインの自動化と運用コスト削減を両立。初期予算では10社分相当のデータ基盤構築相場と比較し、約20%のコストダウンを達成しました。
テスト運用フェーズと成果検証
PoC(概念検証)を終えたテクノプロダクト社は、本格導入前にテスト運用フェーズを設け、約3ヶ月間限定で一部ラインに新システムを並行稼働させました。まずは以下のステップで成果を検証しました。
-
稼働比較:同一機種のラインA(新システム)とラインB(従来メンテ)で故障発生率を比較
-
コスト集計:センサー・ゲートウェイの運用コスト、予備部品発注コストの実績値収集
-
現場ヒアリング:ライン担当者へのアンケートで使い勝手や警告精度を評価
-
レポーティング:月次でKPIをまとめたレポートを経営層へ提出
テスト運用の結果、ラインAでは故障による稼働停止が半減し、月あたり平均稼働時間が20時間(約5%)向上。一方、追加投資したIoT機器・クラウド利用料は月額約15万円で、従来の緊急対応工賃や部品交換費用比で30%以上のコストダウンを確認できました。特に注目すべきは予測警報の誤検知率が10%以下に抑えられた点で、保全チームから「過剰な対応負荷が増えず、費用対効果が高い」というフィードバックを得ています。
このフェーズでの学びとして、データ品質の確保とチュunningの重要性が浮き彫りになりました。具体的には、センサーの取付位置やゲートウェイ前処理ロジックを微調整することで、予測精度が15%向上。こうした継続的なチューニングは、システム、データ基盤にかかる予算管理と併せて考えるべきポイントです。
全社横展開~スケーラビリティ確保
テスト運用の成功を踏まえ、テクノプロダクト社は全7箇所の生産拠点に同システムを展開します。横展開にあたっては、以下の課題と対策を講じました。
-
拠点ごとのネットワーク環境差:VPN構築やMQTTブローカーのリダンダンシー設計で対応
-
センサー・ゲートウェイ調達:複数拠点一括発注によるコストダウン交渉
-
運用体制の統一:SOP(標準作業手順書)を全拠点共通化し、現場に展開
-
データ統合:BigQuery上のデータセットを拠点別・機種別に管理することで相場分析を効率化
展開プロジェクトは約6ヶ月で完了し、導入コストはPoCの1.5倍程度に抑制。これは、拠点横断契約によるセンサー購入費用の相場交渉と、クラウド利用料のリザーブドインスタンス購入を行った成果です。
また、システム負荷増大に備え、クラウド基盤は自動スケーリング設定を導入。ピーク時でも遅延なくダッシュボード表示やアラート送信が可能となり、開発会社との契約にも「可用性SLA」を盛り込むことで、将来予算や費用のブレ幅を最小限にしています。
KPI設計とROI分析
全社横展開後は、投資対効果を継続的に評価するためのKPIを設定。以下の指標を毎月モニタリングしています。
-
ダウンタイム削減率:導入前後での機械停止時間比
-
保全コスト削減額:工賃+部品費+維持費のトータル
-
予測警報精度:誤検知率および未検知率
-
稼働率改善:総稼働時間÷稼働可能時間
-
ユーザー満足度:現場担当者アンケートスコア
これらKPIの結果を基に、ROI(投資利益率)を次の式で算出。
テクノプロダクト社では、初期投資1,350万円に対し、年間コスト削減効果が約5,000万円と試算され、ROIは約270%に。これにより、2年以内の全投資回収が確実視されています。
また、相場観を維持するため、開発会社との協議で「2年後のメンテナンス費用見直し権」を契約に追加。これにより、運用フェーズにおける予算管理やベンダー選び方の柔軟性を確保しています。
維持管理体制の構築とコスト最適化
持続的な運用に向け、以下の体制を構築しました。
-
社内専任チーム設置:中央保全部門に3名をアサイン
-
開発会社による24/7サポート:SLAに基づく障害対応契約
-
定期メンテナンス契約:年間スケジュールにてゲートウェイFWやMLモデルの更新
-
コストモニタリングダッシュボード:クラウド利用料やIoT回線費用をリアルタイム可視化
これにより、予算超過リスクを低減しつつ、事前にトラブルを検知して対策を打つガバナンスが確立。結果として、1年間で運用コストを当初見積より15%最適化でき、開発会社への発注予算も想定相場内に収まりました。
今後の拡張計画:AI+IoTで次世代スマートファクトリーへ
テクノプロダクト社では、IoT予知保全成功を足掛かりに、以下の拡張機能を検討中です。
-
異常自動修正アクション:ロボットアームと連携し、軽微な異常は自動でメンテナンス
-
生産スケジューリング最適化:稼働予測データをWMSに連携し、ライン稼働計画を自動調整
-
品質自動検査連携:予知保全データと製品検査データを統合し、不良率低減に寄与
-
マルチベンダー対応:他社製センサーやPLCにも対応範囲を拡大
これらを実現するには追加予算が必要ですが、既存のクラウド基盤と社内チームを活用することで、最小限の開発会社発注での実装を想定。費用対効果が見込める展開順序を精査し、次年度予算内での遺漏なく発注する計画です。
導入にあたっての注意点とポイントまとめ
本事例を成功に導いた要点を振り返ります。
-
要件定義の明確化:PoCで優先機能を絞り込み、相場に応じた予算設計を実現
-
開発会社選び方:ドメイン経験・柔軟な体制・費用根拠の明示を重視
-
データ品質向上:センサー配置と前処理調整による予測精度最適化
-
スケール戦略:拠点横展開は一括調達とSLA契約でコスト抑制
-
運用ガバナンス:KPI設計・ROI分析・予算管理ダッシュボードによる継続改善
これらを踏まえることで、同様のIoT予知保全プロジェクトでも、システム選定から予算・費用管理、発注後の運用体制構築まで、相場感に基づいた最適な導入が可能になります。ぜひ自社の課題に合わせたユニークな切り口で、次世代スマートファクトリーへの第一歩を踏み出してください。