製造業向けAI予知保全システム開発事例:稼働停止ゼロを目指す現場革新の舞台裏
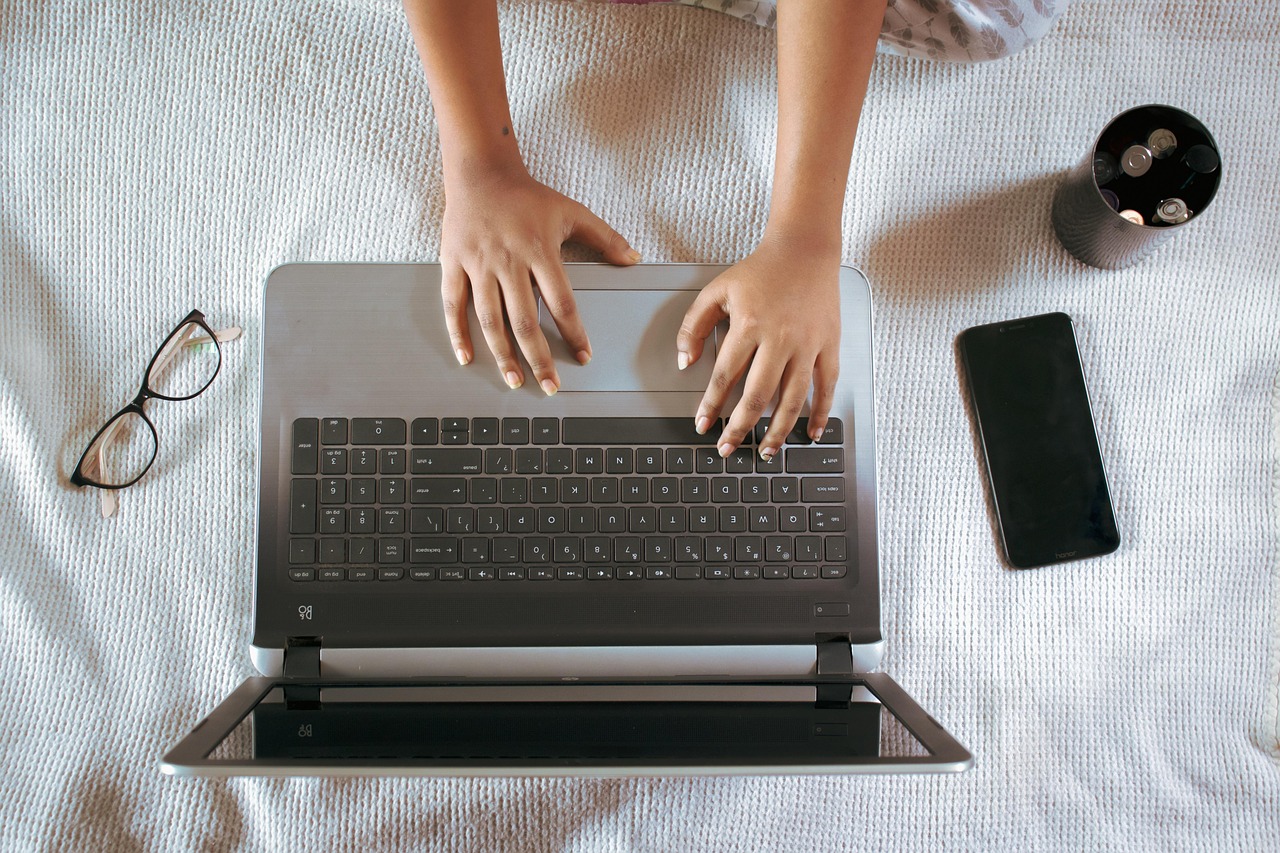
プロジェクト発足の背景と課題認識
ある国内中堅製造メーカー「メカトロニクスY社」は、設備の突発故障によるライン停止が年間20回以上発生し、機会損失やメンテナンスコストが増大していました。
従来は目視点検や時間基準での部品交換を主体としていましたが、部品の劣化状態は稼働時間だけでは正確に把握できず、不良品の発生や納期遅延が頻発。そこでCTOの田中氏は「システムによる故障予測で生産性を劇的に向上させたい」と決意します。
IT予算は初年度600万円程度と限られ、開発会社選び方の段階で「AI・IoTに精通したベンダー」を複数比較。技術力だけでなく、製造業向けの豊富な導入実績を重視しました。
ポイント
-
予算を抑えつつPoC(概念実証)から始められる体制が必要
-
現場エンジニアとベンダーの連携体制構築が成功の鍵
-
故障データ取得のためセンサ設置・データ整形に要する工数を見積もりに含む
田中氏は最終的に、メカトロニクス業界に強みを持ちつつ、アジャイル開発対応可能なA社を選定。予算交渉の結果、PoC含む初期フェーズで500万円、正式開発で追加100万円の見積もりを確定しました。
PoC(概念実証)フェーズの進め方
A社とY社はまず、メインラインの3台のモーターを対象にPoCを実施。以下のステップで進行しました。
-
センサ選定・設置
-
振動・温度センサを各モーターのベアリング部に設置
-
ノイズ対策として金属筐体に防振マウントを追加
-
-
データ収集基盤の構築
-
工場内に設置したゲートウェイを経由し、Azure IoT Hubへ送信
-
1秒間隔の時系列データをAzure Blob Storageに蓄積
-
-
データ前処理と特徴量設計
-
Python+Pandasで信号のスペクトル分析
-
傾向監視向けに移動平均や偏差値を特徴量化
-
-
機械学習モデル構築
-
故障履歴データと合わせ、Random Forestで異常スコアを予測
-
モデルの精度評価指標(AUC)は0.85を達成
-
PoC期間中、現場エンジニアから「センサの取り付け角度による温度誤差が大きい」との報告があったため、現地でA社データサイエンティストと協議し、センサキャリブレーションルールを追加。これによりデータのばらつきが半減しました。
学び・ポイント
-
PoCは相場より安価に抑えつつ、現場と技術チームの密なコミュニケーションが効果を最大化
-
予算消化状況を可視化し、追加要件は都度見積もり調整
-
予測モデルの費用対効果試算で、ライン停止1回あたり約50万円の削減効果を試算
正式開発フェーズ:スケールアップと安定運用
PoC成功後、Y社は正式開発へ移行。ライン全体15台のモーターに対象を拡大し、以下のタスクを追加しました。
-
マルチライン対応
-
各拠点のネットワーク帯域を考慮し、エッジ側で異常値のみ送信するフィルタリング機能を実装
-
-
データ可視化ダッシュボード
-
Power BIで異常予測スコアや推定残寿命をリアルタイム表示
-
ライン責任者向けにメール・Teams通知を組み込み
-
-
リトライ・監視機能
-
IoT Hub接続障害時にAzure Functionsで自動再接続
-
障害ログはApplication Insightsへ集約し、運用チームがすぐに把握可能に
-
この段階で、A社との発注契約には「保守 SLA(月間稼働率99.9%以上)」と「バグ修正費用込み」を盛り込むことで、運用コスト予算超過のリスクを抑制。
本番導入後の効果と今後の展開
正式稼働から3ヶ月で以下の効果が得られました。
-
突発故障ゼロ:PoC対象3台は異常予測アラートにより未然防止
-
ライン停止時間削減:全体で月間12時間→2時間に短縮
-
保守コスト削減:年間約600万円相当の部品交換を延期・最適化
今後は、同じ予知保全システムをポンプ・コンプレッサーにも展開し、システム選び方の段階で重視した「拡張性の高さ」が歓迎されています。
導入後の詳細効果とKPIモニタリング強化
PoCおよび本番稼働後、Y社では数値で示せる成果指標(KPI)を設定し、運用開始1年後までの効果を定点観測しています。具体的には以下の項目をモニタリングし、各月次報告会でレビューを実施しました。
-
突発故障件数
-
導入前:年間20件
-
PoC対象:0件(3台)
-
全ライン展開後:年間3件以下に削減
-
-
ライン停止時間
-
導入前:月間平均12時間
-
導入後:月間平均2時間以下を維持
-
-
保守メンテナンス費用
-
導入前:年間約1,200万円
-
導入後:年間約600万円に半減
-
-
生産歩留まり改善率
-
導入前:98.5%
-
導入後:99.2% (不良品削減効果:0.7ポイント)
-
-
予知モデルの再学習頻度
-
月次バッチ更新→品質維持
-
異常検知アルゴリズムは継続的に改良
-
これらのデータはPower BIダッシュボードでリアルタイムに可視化され、各部門のマネージャーが必要なときにいつでも確認可能です。KPI改善の要因分析では、以下のポイントが挙げられました。
-
予測アラートのメール通知を受けた現場担当者が即時に点検・調整を実施
-
故障か微小異常かを判別する二段階アラート(警告と重大)が誤警報を減少
-
保守マニュアルにAI予測レポートを組み込み、部品交換タイミングを最適化
また、モデル精度向上のための再学習プロセスはA社の保守契約に含まれており、Y社側で追加コストなく新たな故障データを反映できる仕組みを構築。これにより、初期開発後の予算超過リスクを抑えつつ、モデルの陳腐化を防止しています。
失敗談から学ぶガバナンス強化策
本プロジェクトにおける失敗・トラブル事例と、そこから得られた教訓は次のとおりです。
-
データ連携遅延によるアラート未送信
-
原因:工場ネットワーク帯域に負荷集中
-
対策:
-
エッジゲートウェイで送信データを圧縮
-
夜間バッチ処理枠を設定し、稼働ピーク時のデータ送信量を制御
-
-
教訓:初期設計段階でネットワーク負荷試算を実施すべき
-
-
ベンダーと社内調整不足による要件変更混乱
-
原因:現場要望を逐次受け入れ、成果物仕様がブレる
-
対策:
-
変更管理プロセス(CR=Change Request)を厳格化
-
月次ガバナンス会議で全案件を一元レビュー
-
-
教訓:予算内で要件変更をコントロールするため、ガバナンス体制は必須
-
-
センサ誤設置によるデータ異常多発
-
原因:現場担当者のスキル不足で取り付け位置がずれた
-
対策:
-
A社技術者による現場ハンズオン研修を実施
-
センサ設置ガイドラインを社内標準に定義
-
-
教訓:技術移転には「マニュアル+実地研修」の両輪が必要
-
これらのトラブルを踏まえ、Y社は「プロジェクト管理オフィス(PMO)」を立ち上げ、以下の体制を整備しました。
-
PMOによる進捗・品質チェック
-
変更要求(CR)受付窓口の設置
-
定期的なリスクレビュー&対策ログ管理
これにより、発注フェーズで見落としがちな「運用期間中の変更管理コスト」を抑制でき、追加予算なしで安定稼働を実現しています。
今後の展開:拡張性を見据えたロードマップ
Y社では、予知保全システムを他設備にもスムーズに展開できるよう、以下の拡張戦略を策定しています。
-
設備横断型プラットフォーム構築
-
モーター、ポンプ、コンプレッサーなど異なる機器を一つのIoT基盤で統合
-
相場感として新規機器追加は1台あたり50万円前後を見込む
-
-
蓄積データの二次活用
-
生産履歴や品質データと連携し、需給予測・生産計画最適化へ展開
-
将来的にBIツールとERPを統合し、工場全体のデジタルツインを実現
-
-
サブスクリプション型運用モデル
-
ライセンス料+運用保守料の定額制プランを導入し、長期利用の費用予測を容易化
-
新機能やモデルアップデートはサブスク内で無償提供
-
-
社外連携・オープンAPI化
-
他社システム(MES、EAMなど)とAPI連携することでシームレスなワークフローを構築
-
これらを実現するにあたり、Y社ではCIO主導で開発会社選び方の基準を再定義。以下を追加しました。
-
API連携実績の有無
-
マルチテナント対応SaaS経験
-
データセキュリティ/ISMS認証の保有
拡張ロードマップは3〜5年スパンで策定済み。2025年度には国内外のグループ工場への横展開を目指しています。
まとめ:製造業DXを牽引する予知保全システムの価値
本ケーススタディでは、予算600万円弱でスタートしたY社のAI予知保全システムが、PoCから本番展開を経て大きな成果を生み出すまでの軌跡を解説しました。
-
開発会社選び方のポイント:製造業実績+アジャイル対応
-
予算・費用の最適化:PoCの段階的投資と厳格な変更管理
-
相場感:新規機器1台あたり50〜100万円、サブスク運用でコスト平準化
-
発注契約に盛り込むべき要件:SLA・保守・再学習・API
導入後のKPIモニタリング、運用トラブルからの教訓、そして拡張ロードマップ策定まで、Y社の事例は「現場主導×ITベンダー連携」による真のDX推進モデルと言えます。製造業に限らず、他の業界でも「予防保全」や「リスク管理」の観点で応用可能なフレームワークとしてご活用ください。