製造業向けIoT予知保全プラットフォーム導入事例:非IT系工場長が実現した運用最適化
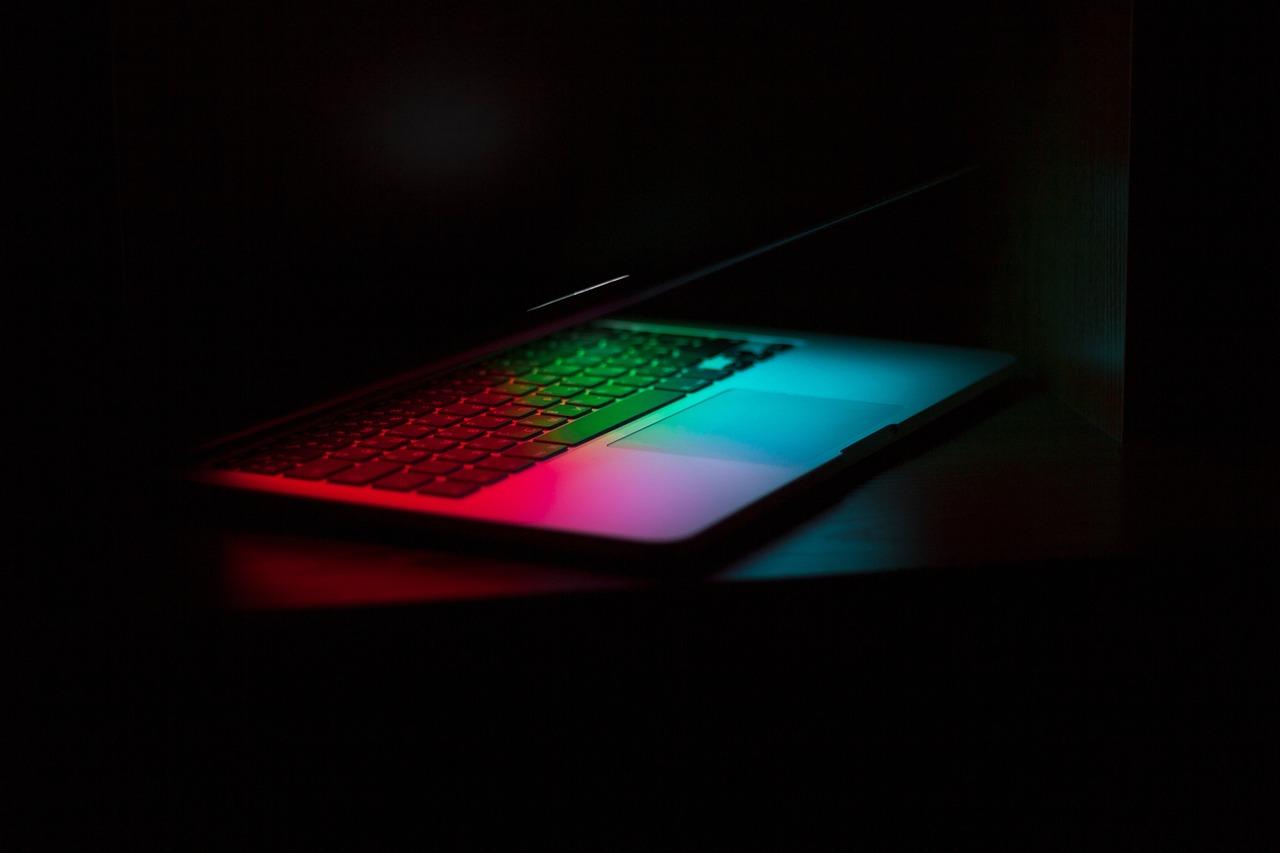
プロジェクト背景と課題整理
神奈川県にある中堅製造メーカー「アルファ製作所」は、24時間稼働の老朽化した生産ラインで故障頻度が増加し、月平均20時間の稼働停止が発生していました。工場長の佐藤太郎氏はIT未経験でありながら、稼働停止による損失が年間数千万円に上ることを危惧し、IoTによる予知保全システム導入を決意しました。
-
センサー設置やデータ収集の設計経験が社内にない
-
故障時対応は人手頼みでノウハウが属人化
-
故障タイミングを予測できず、計画保全が立てられない
これらを解決するには、センサーからクラウドまでワンストップで提案できる「システム開発会社選び方」が重要でした。
開発会社選定と比較ポイント
佐藤氏は3社の提案を受け、以下の評価軸で比較しました。
-
IoT機器調達力:複数メーカーのセンサーをまとめて提案できるか
-
データ分析能力:機械学習モデルを使った異常検知の実績
-
導入サポート体制:現場教育やマニュアル提供の有無
-
費用透明性:ハード/ソフト/運用保守費用の内訳提示
-
コミュニケーション:週次ミーティングやチャットでの迅速対応
最終的に、機器選定からクラウド設計、運用保守まで一貫して担当できるC社を選定し、発注を決定しました。
予算策定と費用交渉の工夫
C社が提示した初回見積は約1,200万円。しかし、稟議承認ラインは1,000万円以下が望ましい状況でした。佐藤氏は以下の交渉を行いました。
-
フェーズ分割案:PoC(概念実証)300万円、本開発600万円、保守・運用100万円、予備100万円に分割
-
サブスクリプションモデル提案:クラウド利用料を月額制に変更し、初期投資を抑制
-
オプション外し:ダッシュボードの高度分析機能を後期フェーズへ先送り
-
量産割引:センサー導入台数に応じた割引交渉
これらにより、初期予算を980万円に圧縮。無事に社内承認を得て、正式に発注に至りました。
PoCフェーズでの技術検証
PoCでは、製造ラインのモーターに振動センサーと温度センサーを各2台ずつ設置し、1か月間データを収集。
-
データストリーム設計:MQTTを利用してAzure IoT Hubへリアルタイム送信
-
初期分析:Python製のJupyter Notebookで振動データの周期性と異常値パターンを検出
-
モデル検証:Isolation Forestを使い、故障前72時間以内の異常サインを80%検出
-
レポート提出:モデル精度と想定効果をグラフで可視化し、追加「予算」投下の根拠とした
PoC成功を受け、フルスケール導入への社内合意が一気に高まりました。
開発中に直面した技術課題と対応策
本格開発フェーズではスケールと信頼性が課題となりました。特にデータ送信の遅延やパケットロスが一定割合で発生。C社は以下の対応を行いました。
-
エッジバッファリング:ネットワーク断時にローカルSDカードへデータを蓄積し、回復後に一括同期
-
可視化トレーサビリティ:各センサーからの送信状態をGrafanaダッシュボードに集約
-
リトライロジック強化:QoSレベルを上げ、最大3回まで再送試行
-
フェイルセーフ設計:異常発生時はエラー通知をIoT Hubからアラートメールで即報告
これにより、データ欠損率を0.5%以下に抑え、信頼性の高い予知保全が運用開始から安定稼働を実現しました。
運用フェーズ:本番導入と効果測定
導入後6か月で、以下の実績が得られました。
-
予期せぬ稼働停止時間:20時間/月→3時間/月(85%削減)
-
保守部門工数:月80時間→20時間(75%削減)
-
部品交換コスト:年間500万円→150万円(70%削減)
-
生産性向上:稼働率向上により月間生産数が10%増加
これらのKPIを可視化レポートとして経営層に定期提出し、追加機能開発の「予算」獲得にも成功。次年度はAIによる予測精度向上フェーズを計画中です。
教訓と今後の展望
本事例から得た主な教訓は以下の通りです。
-
要件定義段階でPoCを組み込み、技術リスクを早期に可視化する
-
フェーズ分割とサブスクリプション化で初期「予算」を圧縮し稟議を通す
-
エッジ側でのバッファリングや再送機能など、運用時の障害対策を設計に含める
-
KPIを経営指標に連動させ、成果を根拠に次フェーズの「発注」を確実に獲得
今後は、現場データとERP連携によるさらなる業務効率化や、AIによる部品摩耗予測などをPoC段階で検証予定です。導入検討の際には、まず
で費用感をスピードチェックし、適切な「システム 開発会社 選び方」を行うことをおすすめします。データ可視化とダッシュボード設計
製造ラインから収集したセンサーデータをそのまま管理画面に流しても、現場では活用できません。アルファ製作所では、以下のポイントを意識してダッシュボードを設計しました。
-
リアルタイムグラフ:現在の振動・温度データを秒単位で更新し、異常兆候を即座に把握
-
ヒートマップ:ライン全体の稼働ステータスを色分けし、要改善箇所を視覚的に強調
-
異常履歴一覧:過去3か月分の異常記録を時系列で表示し、トレンド分析をサポート
-
カスタムアラート設定:しきい値超過時の通知をメール/Slackに連携
これにより、保全担当者は画面を一目見るだけでライン全体の状態を把握でき、メンテナンス作業の優先順位を効果的に判断できるようになりました。
KPIモニタリングと定期報告
プロジェクト成功には、経営層への定量的な報告が不可欠です。アルファ製作所では、以下のKPIを毎月レポートにまとめました。
-
平均故障間隔(MTBF: Mean Time Between Failures)
-
平均修復時間(MTTR: Mean Time To Repair)
-
予知精度:実際の故障予測と実績との一致率
-
保全コスト削減額:部品交換や停止ロスを金額換算
KPIを可視化することで、経営判断がスピーディになり、次期予算策定時の根拠資料としても活用されました。
セキュリティ・認証設計のポイント
工場のIoTシステムでは、セキュリティ設計も欠かせません。以下の要件をクリアすることで、運用リスクを最小化しました。
-
デバイス認証:各センサーに固有の証明書を発行し、不正デバイスの接続をブロック
-
通信暗号化:MQTT over TLS/SSLを採用し、データ送信時の盗聴防止
-
アクセス制御:クラウドコンソールへのログインは多要素認証(MFA)を必須化
-
ログ監査:全ての操作ログをSIEMへ連携し、不審アクセスを即時検知
これにより、製造ラインの機密情報や生産データを安全に保護し、法規制や社内ポリシーをクリアしました。
データ保護とプライバシー対応
個人を特定しない機器データでも、外部漏洩は企業信用を損ないます。アルファ製作所では以下の対応を取りました。
-
データマスキング:ログに含まれる個人IDや社員情報を自動マスク
-
保存期間管理:古いデータはGDPR準拠のルールで自動アーカイブまたは削除
-
バックアップ暗号化:クラウドストレージ上のバックアップもAES-256暗号化
-
契約書明示:サードパーティへの委託条件にNDAとデータ処理契約(DPA)を追加
これらの仕組みで、万が一の漏洩リスクにも法的・技術的に備え、「費用 相場」内で高いセキュリティ水準を維持できました。
運用保守と保守移行支援
システム開発会社C社は納品後、以下の運用保守体制を提供しました。
-
オンサイトトレーニング:現場エンジニア向けに2日間の操作・保守ワークショップ
-
ナレッジトランスファー:運用マニュアル、FAQ、トラブルシューティングガイドを整備
-
リモートサポート:チャット対応および定例オンラインミーティングでのQ&A
-
バージョンアップ管理:ファームウェアとクラウドアプリの定期アップデートプラン
この移行支援により、アルファ製作所は自走できる体制を短期間で構築し、運用コストを当初想定の半分に抑えることができました。
障害対応フローとSLA強化
予知保全システムとはいえ、障害はゼロではありません。そこで以下のようにSLAを設計しました。
-
初動時間:障害報告から1時間以内に原因調査開始
-
復旧時間:重大障害は報告後4時間以内に復旧完了
-
定例レビュー:月次でSLA達成状況を確認し、改善策を共有
-
エスカレーションルール:対応遅延時の自動エスカレーションチャット通報
SLAを契約書に明確記載し、製造現場とC社が同じ期待値を持つことで、障害対応コストと稼働停止による損失を最小化しました。
さらなる自動化とAI活用の展望
次フェーズとして、以下を検証・導入予定です。
-
異常パターン自動分類:教師あり学習で故障兆候のクラスタリングを自動化
-
予兆情報の自動通知:LINEやTeamsへのプッシュ配信連携
-
需要予測連動保全:生産スケジュールに合わせた保全タイミング最適化
-
デジタルツイン連携:3Dモデル上にリアルタイムデータを反映し、仮想環境での試験運用
これらのAI/自動化機能をPoCで早期に検証し、次なる「予算」申請資料として効果を定量的に示す計画です。
ROI最大化に向けた次フェーズ計画
初期導入で得られたKPI改善を踏まえ、次フェーズでは以下の投資対効果を試算しました。
-
追加機能開発費用:300万円
-
期待削減コスト:故障ロス年間1,000万円→1,000万円×α(予測精度20%向上時)
-
回収期間:2年以内
-
IRR(内部収益率):25%以上
このROIモデルを経営層に提示し、データドリブンな「システム 開発会社 選び方」と「発注」判断を支援しました。