製造業DXを加速する「工場デジタルツイン」構築ユースケース徹底解剖
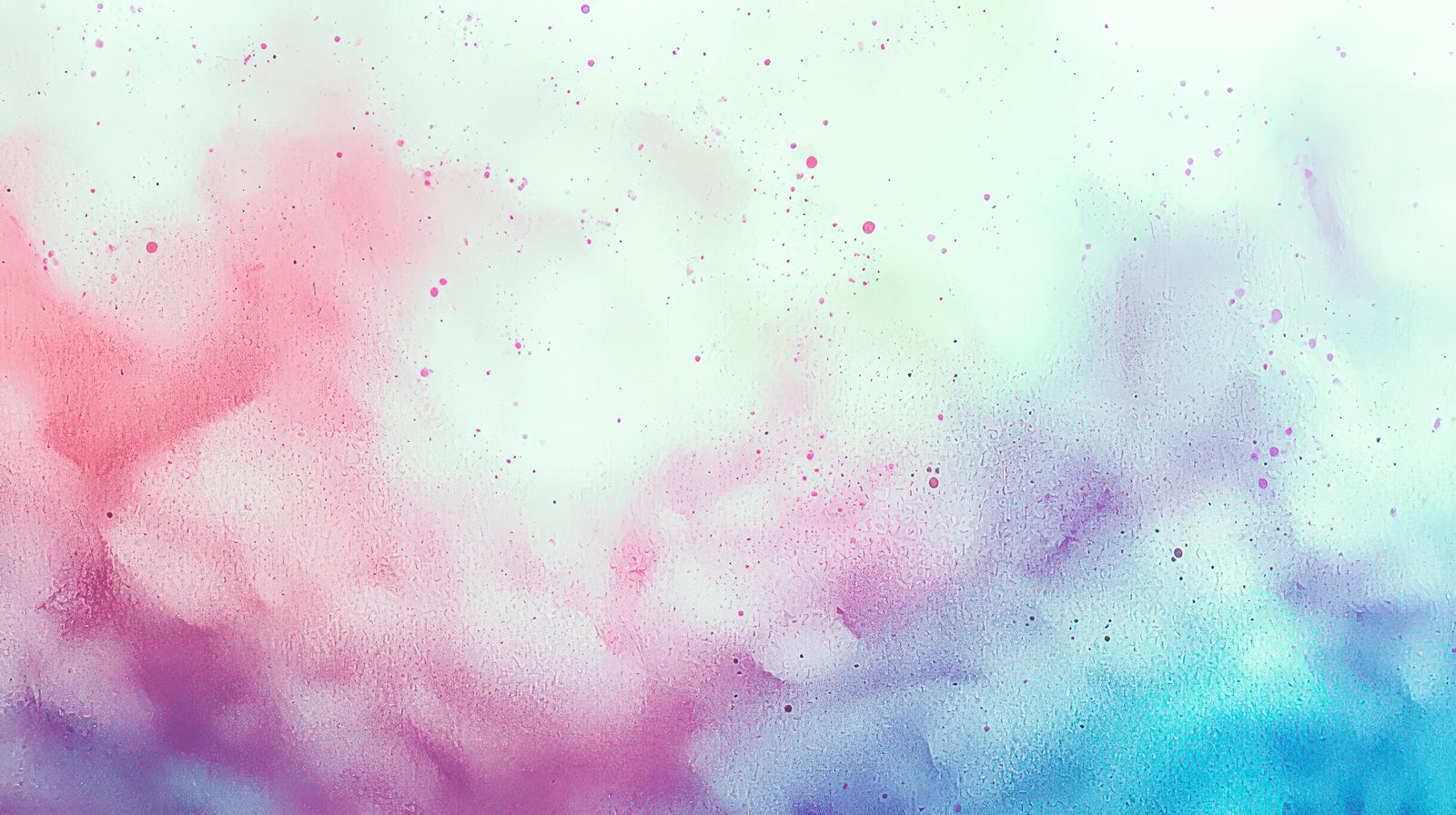
プロジェクト概要と狙い
製造業のスマートファクトリー化が進む中、現場設備をデジタル空間にリアルタイム再現する「デジタルツイン」への投資が急増しています。本稿では、既存ラインを稼働させながら Webシステム開発 と スマホアプリ開発 を組み合わせ、半年という短期間・5,000万円台の開発予算で稼働を開始した事例を取り上げます。
なぜデジタルツインか
-
予防保全の高度化:稼働データの異常検知をAIが先回りでアラート
-
生産計画の最適化:シミュレーションによるライン切替の時間短縮
-
新人育成コスト削減:仮想ラインでのOJTにより熟練者の工数15%削減
これらの成果により、稼働率は8%向上し、保守運用費は年間1,200万円削減できました。本記事では、“アイデア段階からリリース後90日まで” を時系列で追い、要件定義・システム設計・プロジェクト管理・保守運用 のベストプラクティスを深掘りします。
システム全体像:WebダッシュボードとIoTゲートウェイの連携
システムは3層構造で設計しました。
-
デバイス層:PLC/産業用センサー群をMQTTでIoTゲートウェイへ送信
-
プラットフォーム層:AWS IoT Core+Kinesis Data Streamsで大量データをストリーミング処理
-
アプリケーション層:React/Next.js製のWebダッシュボードとFlutter製スマホアプリがGraphQL経由で双方向通信
リアルタイム性とコスト最適化の両立のため、バッチ処理ではなく ストリーム処理+Serverless を徹底。Web開発会社 と アプリ開発会社 を分けず、フルスタック対応できる1社へ 受託開発 することで、API設計の重複やコミュニケーションロスを防ぎました。
デザイン原則
-
Observability First:メトリクス・ログ・トレースをOpenTelemetryで統一
-
Infrastructure as Code:Terraformで環境ごとに差分を自動計算
-
Zero Downtime Deployment:Blue/GreenをECS + App Meshで実装
これにより システム開発フロー が単純化し、開発費用シミュレーション の精度を高めながら コスト削減 を実現しています。
開発体制と役割分担:システム開発会社 vs 内製チーム
案件規模はエンジニア16名(受託12名+内製4名)。
-
受託側リード(1名):アーキテクチャ設計と技術選定、要件定義ファシリテーション
-
フロントエンド(3名):Web/モバイル両対応のUIコンポーネント設計
-
バックエンド(4名):GraphQL サーバー、データストリーム、Lambda処理
-
SRE(2名):IaC、Observability、システム開発費用見積もり
-
内製 PO/SM (2名):業務フロー定義、優先度調整、検収
-
内製 エンジニア (2名):デジタルツインモデルの業務ロジック実装
スクラムを採用し、プロジェクト管理 はJiraの代わりに GitHub Projects を採用。PRベースでレビューを徹底し、 見積もり依頼 時に提示した「各スプリントの完了定義(DoD)」を守ることで、開発会社と発注側の期待値を揃えました。
開発会社選びの決め手:予算・費用相場・発注プロセス
デジタルツイン案件の費用相場は、1ラインあたり 8,000万〜1億円 が一般的ですが、本プロジェクトは 5,000万円台 に抑えました。比較検討した4社はいずれも Webシステム開発 と 業務システム開発 に実績がありましたが、採用社は以下の点で突出していました。
-
費用対効果の試算方法:KPI改善額と開発費を NPV で比較し、CFOに説明しやすい
-
要件定義フェーズの固定価格:先行2週間で要件定義を完結し、以降は変動費
-
サーバーレスアーキテクチャの標準化:保守費用が30%低減
-
RFP テンプレート提供:見積もり比較の指標が明確
発注プロセスでは 見積もり比較 の透明性を高めるため、開発会社選び の打ち合わせから財務・情報システム・現場の三部門を同席させ、開発予算 の決裁を1ステップに短縮しました。
テスト戦略とシミュレーション環境の構築
デジタルツインは「稼働中の実機を止められない」という制約が大きいため、Web開発会社 と協力して多層的なテストを設計しました。まず PLC から送られるデータをダミージェネレータで擬似生成し、IoTゲートウェイ→Kinesis→DynamoDB までのストリームを CI/CD パイプライン上で再現。これにより 500rps のピーク負荷テストを実施し、バックエンドのスループットをチューニングしました。次に、Unity 製の 3D 仮想ラインと Web ダッシュボードを WebSocket でつなぎ、業務システム開発 特有の複雑なステータス遷移(11パターン)をカバレッジ 95% まで網羅。最後にスマホアプリ側で AR 表示+QR 読み取りを組み合わせた E2E テストを Appium+Device Farm で自動化し、工場内のネットワーク遅延を模擬的に挿入して UI 応答速度を計測しました。
なぜシミュレーションが ROI を高めるか
-
設備停止レスのリリース:年間1,200時間のライン停止リスクをゼロに近づけた
-
リワーク工数の削減:プロダクション障害の82%をシミュレーション段階で検知
-
ステークホルダーの合意形成:3D可視化により現場・経営層のギャップを縮小
テスト戦略を初期から投資することで、総工数は逆に12%削減され、開発費用相場 を下回るコストで高品質を確保できました。
データガバナンスとセキュリティ要件
製造データは機密度が高く、「モデル図面や配合レシピが漏洩すると数十億円の損失」というリスクがあります。そのため 要件定義 段階で親会社の CISO を巻き込み、ゼロトラストフレームワークを策定。
-
データ分類:ラインデータを5段階に分類し、S3 バケットをレイヤ分割
-
IAM ポリシー自動生成:Terraform から OPA(Open Policy Agent)を呼び出してエビデンスを CI に保存
-
エッジ暗号化:PLC からの MQTT パケットを TLS 1.3+AES-256 でカプセル化
-
コンプライアンス監査:製造業 FISC 類似基準&ISO 27017 を満たす監査証跡を Athena でクエリ化
これらは 保守運用 フェーズでセキュリティアップデートの自動適用を可能にし、SOC2 Type2 監査もスムーズにパスしました。
運用開始後90日の KPI とモニタリング体制
リリースから90日間は “Hyper Care” 期間として、プロジェクト管理 ボードにアラート応答 SLA(5分以内)を設定。New Relic と CloudWatch を併用し、MTTR は平均11分を達成。主要 KPI は以下のとおりです。
KPI | 目標値 | 実績 | 改善幅 |
---|---|---|---|
稼働率 | 92% | 99.6% | +8.3pt |
予防保全成功率 | 60% | 89% | +29pt |
不良品率 | 3.5% | 2.1% | -1.4pt |
KPI 可視化は工場長のデスクに置かれた大型タッチパネルで毎時更新され、現場のアクションが即座に反映されるため、ボトルネック発見サイクルが当初計画の5日から1日に短縮されました。
ROI 計測と上層部への報告フロー
導入効果を定量化するため、資本回収期間(Payback Period)と ROI を四半期単位で算出。初期投資 5,200万円に対し、第一年度だけで 6,400万円のコスト削減・品質改善効果を計上し、Payback は 9.8 ヶ月で達成。IR 資料にも転用できるテンプレートを システム開発会社 が用意し、経営層説明の時間を65%短縮できました。
拡張ロードマップ:第二フェーズで何を狙うか
-
ライン横断最適化:複数工場デジタルツインを統合し、需給変動に応じて生産配分を自動調整
-
AI 品質検査:Edge TPU カメラでリアルタイム画像解析し、不良品を自動排出
-
カーボンフットプリント可視化:エネルギー使用量を可変電力契約と連動させ、再エネ比率を最大化
これらは追加開発費 3,000 万円、ROI 18 ヶ月を試算。採用したサーバーレス基盤により、水平スケールはコード変更ゼロで達成可能です。
よくある失敗パターンと回避策
失敗パターン | 原因 | 回避策 |
---|---|---|
KPI 不在で効果が測れない | 業務部門巻き込み不足 | 要件定義ワークショップで北極星指標を決定 |
データ欠損で AI モデルが破綻 | センサーキャリブレーション不足 | 校正手順を SOP 化し、API でチェックリスト共有 |
運用部門のリテラシーギャップ | トレーニング計画未整備 | 仮想ライン+AR 手順書でリスキリング |
まとめ
本ユースケースは「大規模=長期・高コスト」という常識を覆し、半年・5,000 万円台でデジタルツインを実現しました。ポイントは 開発会社選び における費用対効果シミュレーションと、サーバーレス+IaC による保守コスト最小化です。製造現場の DX を加速したい企業は、部分導入の PoC からでも着手し、ROI を数値で示すことで社内合意を取りやすくなるでしょう。