デジタルツインで製造ラインを劇的改善──スマート工場導入ユースケース完全解説
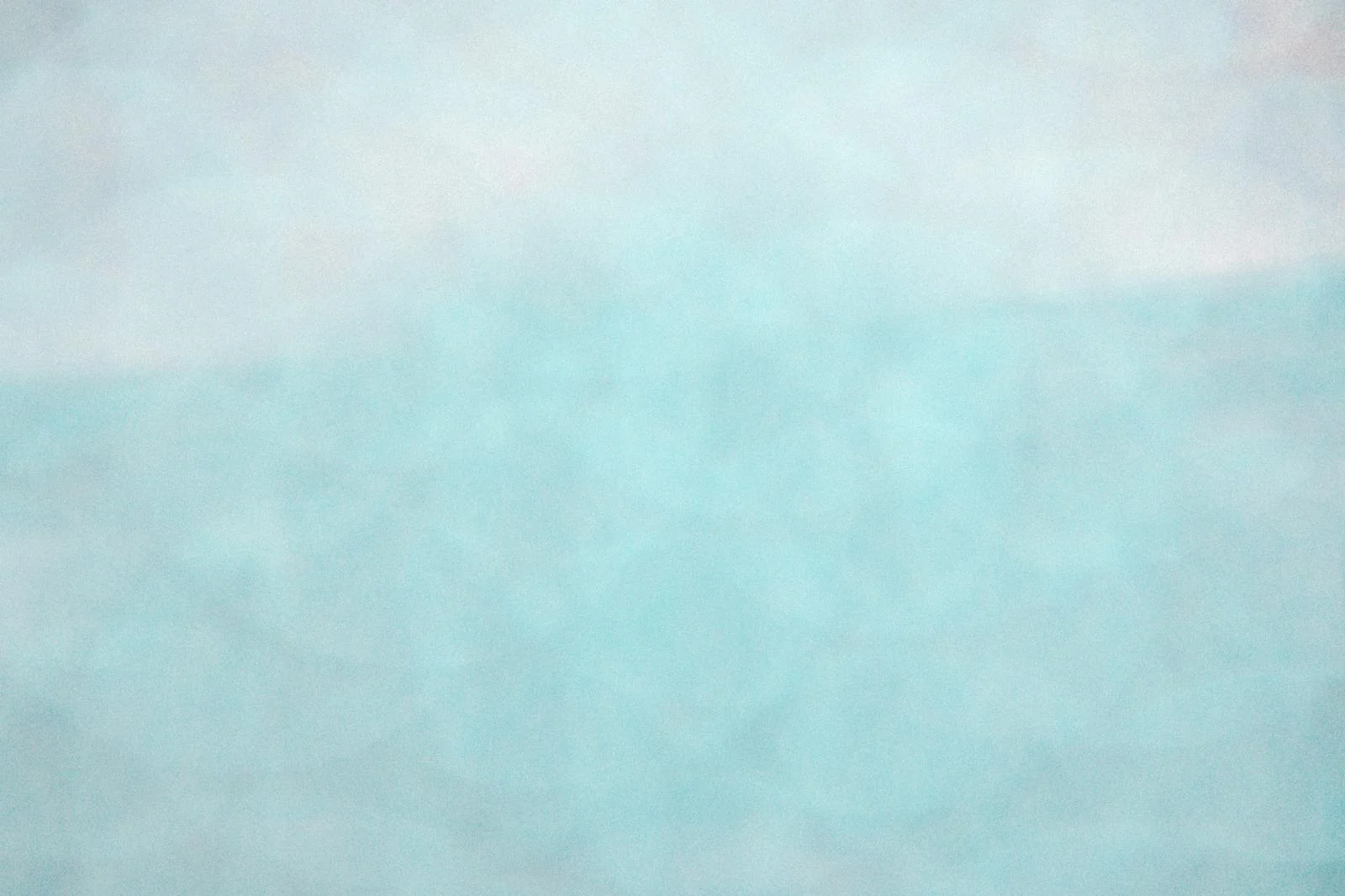
プロジェクトの全体像とビジネス背景
製造業の DX(デジタルトランスフォーメーション)は、単なる機械の自動化では終わりません。IoT センサーとクラウドプラットフォームを組み合わせ、現実の工場をリアルタイムに仮想空間へ写し取る『デジタルツイン』こそが、次世代スマートファクトリーの核心です。システム開発会社に『スマート工場化』を発注しようと考える経営層・情報システム部門の多くは、
-
● 生産効率を 10〜30% 向上させたい
-
● 設備保全コストを可視化し、予算の最適化を図りたい
-
● 属人的なオペレーションを標準化して海外拠点へ横展開したい
という明確な経営課題を抱えています。ところが実際の見積もり依頼段階では、デジタルツインの定義や ROI 指標が曖昧なまま RFP が発行されるケースも散見されます。まずはユースケース全体像を解像度高く描き、プロジェクト計画・開発費用・選定基準を一本の線で結ぶことが肝心です。
デジタルツイン×IoT が創出する三層の価値
デジタルツイン導入プロジェクトでは、価値創出レイヤーを《収集》《統合》《最適化》の 3 層に分けると理解しやすくなります。
収集レイヤー
温度・圧力・振動などのセンサーデータを、エッジゲートウェイで MQTT 配信。Webシステム開発経験のある SIer なら、データスキーマ定義と暗号化チャネルの実装が迅速です。
統合レイヤー
クラウド(AWS IoT Core/Azure Digital Twins など)でメッセージブローカーを介し、データレイクへストリームインジェスト。ここで重要なのは、デジタルツインの仮想モデル(Twin Model)と物理アセットの一意なマッピングです。
最適化レイヤー
機械学習で異常検知モデルを運用し、設備故障を 48 時間前に予兆検知するなど具体的な KPI を設定。プロジェクト管理ツール内で MLOps パイプラインを CI/CD と同等レベルの品質基準で管理します。
これら 3 層がスムーズに接続されて初めて、スマホアプリ開発で培われた UX ノウハウを活かし『スマートダッシュボード』をエンジニア以外の現場作業者へ提供できます。
要件定義フェーズで躓きやすい 5 つの論点
システム開発依頼を行う前に、以下の論点を社内で握れているか確認しましょう。
-
《設備 ID 採番ルール》── PLC メーカー依存のアドレスをどう抽象化するか
-
《データ保持ポリシー》── 動画像や 1 秒間隔テレメトリを何日残すのか
-
《ネットワーク冗長》── 5G SA 導入か有線バックアップか
-
《オンプレ ⇄ クラウド通信経路》── OPC-UA トンネリングか REST/HTTPS か
-
《権限モデル》── 製造部門・品質保証・外部ベンダーのアクセス分離
開発会社を選ぶ際、これらが提案書に明文化されているかを重視すると、プロジェクト開始後の追加見積もりを最小化できます。
スマートファクトリー実装の技術スタック早見表
層 | 推奨 OSS / SaaS | 役割 | 開発費用相場(目安) | 代替案 |
---|---|---|---|---|
センサー & ゲートウェイ | EdgeX Foundry, BalenaOS | データ収集・前処理 | 100〜300万円/ライン | Azure IoT Edge |
データブローカー | Kafka, AWS Kinesis | 高速ストリーミング | 200〜400万円/年 | Google Pub/Sub |
デジタルツイン基盤 | Azure Digital Twins, NavVis IVION | 仮想モデル管理 | 500〜1500万円 | Siemens Digital Twin |
ダッシュボード | Grafana, Superset, React + Three.js | 可視化 & KPI | 300〜600万円 | Power BI, Tableau |
MLOps | Kubeflow, SageMaker | 予兆保全アルゴリズム | 400〜800万円/年 | MLflow on Databricks |
開発会社の見積もり比較を行うときに、この表を埋めて価格差と技術フィットを見極めると、費用対効果が一目瞭然になります。
予算策定──“一次見積もり+段階追加”方式でリスク分散
デジタルツイン案件は、PoC→パイロット→全社展開の 3 段階に分けて発注するのが定石です。一次見積もりでは PoC と最小限のダッシュボード開発のみを依頼し、そこで得た測定値を基に追加開発費をシミュレーション。
-
PoC:2000 万円
-
パイロット(1 工場):6000 万円
-
全社展開(5 工場):2.5 億円
という順で、段階的にコストを可視化しながら進行すると、CFO の承認プロセスが通りやすくなります。
導入スケジュールとプロジェクト管理手法
Gantt チャートではなく、スクラム + ステージゲートのハイブリッドを推奨します。要件が動的に変わる IoT 領域で、古典的ウォーターフォール一本やりはリスクが高いからです。
-
0〜2 週:要件定義スプリント
-
3〜8 週:データ収集 & ブローカー構築
-
9〜16 週:デジタルツイン PoC & KPI 設定
-
17〜24 週:MLOps パイプライン & ダッシュボード
-
25 週以降:パイロット稼働 & 効果測定
各ゲート終了時に経営レイヤーが Go/No-Go を判断できる成果物(動画デモ・KPI レポート)を用意することが、プロジェクト継続の鍵となります。
ステークホルダー別メリットと導入後の変化
-
経営層:原価低減率が月次レポートで可視化され、投資意志決定が迅速化
-
工場長:ライン停止前にアラートが上がり、計画外ダウンタイムが 40% 減少
-
情報システム部:GitOps 化により構成変更が Pull Request ベースとなり、監査工数が半減
-
品質保証部:不良品率と設備パラメータの相関がダッシュボードで即確認可能
これらのメリットを社内で“共通言語化”しないまま開発会社へ丸投げすると、想定効果を得られないまま移行費用だけが膨らむ恐れがあります。
現場実装で直面した技術的ボトルネック
デジタルツインの PoC が成功しても、量産ラインへスケールする段階では予期せぬ技術的ハードルが噴出します。最大の難敵は「レガシー設備の通信プロトコル断絶」です。1970 年代に導入された NC 旋盤や射出成形機は RS-232C や独自バイナリでデータを吐き出すため、ゲートウェイに追加変換モジュールを実装せねばなりません。変換モジュールが増えるほど遅延・故障点が増え、MTBF(平均故障間隔)が短縮──結果としてライン停止リスクが高まります。
次に挙げられるのが「時刻同期」。センサー時刻が 500 ms ずれるだけで、機械学習モデルは誤った因果関係を学習し、誤検知アラートを乱発しかねません。NTP では誤差が残るため、IEEE-1588 PTP を Gigabit スイッチでフルサポートする必要があります。これを後から対処すると、スイッチ入れ替え費用が 1000 万円規模になることも珍しくありません。
さらにクラウド転送帯域の確保も無視できません。高精細動画ストリームを 30 台のカメラから毎秒 10 Mbps で送信すると、それだけで 3 Gbps。WAN が飽和すれば全社ネットワークの SLA を毀損します。エッジ AI で推論まで局所実行し、異常ポイントの切り出しフレームのみをクラウドへアップロードするといった帯域シェービング設計が不可欠です。
ベンダー選定チェックリストと RFP の書き方
システム開発会社を選ぶとき、表面的な PoC 実績だけで決めると痛い目に遭います。下記 7 項目を RFP(提案依頼書)に盛り込み、各社の回答を比較してください。
-
ツインモデル作成ツールの自動生成機能──CAD 図面や BIM データからスキーマ変換できるか。
-
エッジ側 OTA 更新──稼働中ゲートウェイをダウンタイム無しでアップデートできる仕組みの有無。
-
双方向制御──ツイン空間でパラメータを書き換えたとき、実機へ安全に反映できるロールバック設計。
-
CI/CD と MLOps の統合──GitHub Actions 等でデプロイを一元管理し、再現性を担保できるか。
-
海外拠点ローカリゼーション──時差・言語・法規制を踏まえたアーキテクチャ提案の実績。
-
総保有コスト試算(TCO)──5 年間の運用費・ライセンス費を含むシミュレーションを提示できるか。
-
退出オプション──プロジェクト終了時にデータとモデルを持ち帰れるエクスポート機能の提供。
RFP には KPI とペナルティ条項を明記し、プロジェクト管理上の曖昧さを排除しましょう。
事例紹介:中堅自動車部品メーカー A 社の導入ストーリー
A 社(従業員 1,200 名)は、ベテラン技術者の退職と同時に歩留まりが急落し、経営陣がデジタルツイン導入を決断しました。まず 15 台のサーボプレス機に加速度センサーとマイクを装着。異常音と振動パターンを AI が解析し、金型摩耗を 72 時間前に検知する PoC を 12 週間で実施しました。
結果、年間 4 回発生していた突発停止がゼロに。生産ロス削減額 1.3 億円/年に対し、PoC 費用は 3500 万円。ROI は 3.2 か月で黒字転換しました。同時にデータ取得のために導入した 5G SA ネットワークが社内インフラ刷新を加速し、MES(製造実行システム)との統合もスムーズに進行。第二工場への横展開を決定するまでに要した期間はわずか 6 か月でした。
この成功要因は「段階発注」と「社内 KPI の数値化」にあります。経営会議でリアルタイムに KPI ダッシュボードを投影し、費用対効果を誰でも確認できる体制を構築したことで、現場と経営の温度差を解消できました。
コスト最適化シミュレーションと ROI 算定モデル
デジタルツイン案件のコストは、
-
固定費:センサー購入・ネットワーク工事・クラウド初期設定
-
変動費:データ転送量課金・ストレージ・モデル再学習
に大別されます。ROI を説得力ある形で提示するには、設備稼働率(OEE)の向上率を中心指標に据えましょう。数式は以下です。
例えば OEE を 7 ポイント改善、利益率 18%、売上 100 億円、導入コスト 2 億円なら、
(0.07×0.18×100億−2億)÷2億 ≒ 5.3=530% の投資効果となります。
ROI が 300% を超えれば CFO の稟議も通りやすくなり、資金調達も有利です。
保守運用フェーズで差がつく監視・アラート設計
運用開始後の失敗で多いのは「通知が多すぎて誰も見なくなる問題」。アラートは三段階にレベル分けし、チャットツール連携で即応グループを明確にします。
-
Info:定期レポートのみ(週次)
-
Warning:担当ライン長へ DM(1 時間以内対応)
-
Critical:24 h コールセンター&管理職へ電話連携(15 分以内対応)
さらに**SRE(Site Reliability Engineering)**の考え方を製造業へ応用し、SLO(Service Level Objective)を「稼働率 97%、アップロード遅延 5 秒以内」など数値化。エラー・バジェットを超えたら新機能開発を停止し、信頼性改善に全リソースを振り向ける体制を敷くと長期運用が安定します。
拠点横展開のロードマップとガバナンス体制
1 工場で成功しても、他拠点にコピーする際にはガバナンスが必須です。
-
テンプレート Git リポジトリ:IaC(Infrastructure as Code)のコードを工場別ブランチで管理
-
Change Advisory Board:変更申請を週次でレビューし、標準逸脱を抑制
-
データ主権対策:国境を跨ぐ場合、EU GDPR や中国 MLPS など各国規制を踏まえてリージョン分散。
同じクラウドでも、リージョンが異なるとサービス SLA が変動する点に注意しましょう。
デジタルツインと SDGs/ESG 経営の接点
エネルギー消費量のリアルタイム可視化により、CO₂ 排出をライン単位でモニタリングできます。ISO 50001(エネルギーマネジメントシステム)の監査では、『実在データに裏づけられた改善措置』を提出する必要があるため、デジタルツインは ESG 報告の裏付けとしても強力です。
また、サプライチェーン全体の環境負荷をシミュレーションできるため、Scope 3 排出量の削減計画を投資家へ提示しやすくなります。持続可能性は資金調達コストに直結するため、金融機関向けプレゼン資料にデジタルツインの実績を盛り込む企業が増えています。
まとめと次のアクション
デジタルツイン導入は、IoT や AI の寄せ集めではなく、**経営・現場・IT 部門が同じ KPI を共有するための“共同作業基盤”**です。
-
まずは PoC の ROI を 3 か月以内に示せる小規模範囲を選定。
-
予算策定は段階発注方式で CFO 承認プロセスを滑らかに。
-
RFP には Twin モデル自動化や MLOps 統合など 7 項目を必ず盛り込む。
-
保守運用ではアラートレベルと SLO を明確にし、SRE 的アプローチを導入。
-
SDGs/ESG 報告書へ数字を盛り込み、企業価値を高める。
これらを一貫して牽引できるシステム開発会社を選べば、スマートファクトリー化は単なるコストではなく、経営レバレッジとして機能します。今こそデジタルツイン導入を検討し、次世代ものづくり競争へ一歩先んじましょう。